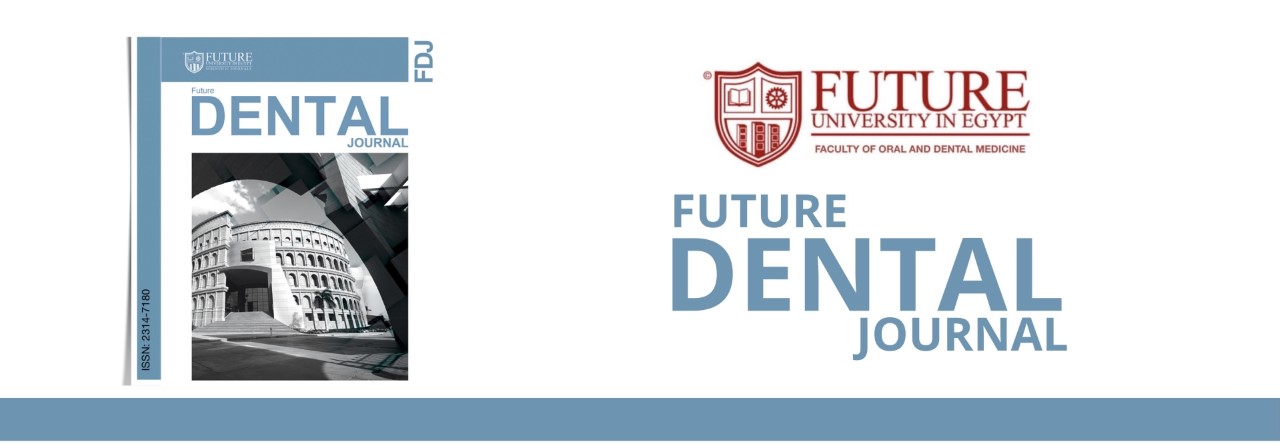
ORCID
https://orcid.org/0000-0002-0593-1686
Abstract
Aim: The aim of that study was to evaluate the marginal and internal fit of a 3-unit, and 6-unit interim fixed dental prosthesis manufactured through milling and 3D printing technologies. Materials and Methods: Forty-eight interim fixed dental prostheses (FDP) were equally divided into two groups according to the fabrication technique. In group (MT), specimens were fabricated through milling technology while in group (PT), specimens were obtained by 3D printing. Each group was subdivided equally according to the FDP span length into 3-unit FDP (SFDP), and 6-unit FDP (LFDP). Marginal and internal fit were measured through the superimposition of the digital master model data and data of the fitting surfaces of the milled and printed FDPs using the “best-fit” alignment feature of a 3D evaluation superimposition software. The Mann-Whitney U test was used to compare the two fabrication techniques as well as the two span lengths. The significance level was set at P < 0.05. Results: Results showed that 3D printing showed statistically significantly higher overall marginal gap distance (MGD) than the milling technique for the (SFDP) subgroup while milling showed higher overall (MGD) values than 3D printing for the (LFDP) subgroup. For internal fit, 3D printing showed lower overall internal gap distance values than milling. Conclusions: Milling technology was able to produce restorations with better marginal fit compared to 3D printing only in 3-unit FDPs. However, the opposite was true when the internal fit of the restorations was considered where 3D printing surpassed the milling technique in both the short-span and long-span FDPs. Consequently, 3D printing could be the technique of preference for fabricating provisional restorations especially when it comes to complex long span FDPs.
Recommended Citation
Shalaby MA, Wahba MM, Al-Ansari HI, Mohamed AN. Assessment of the Effect of two Different Digital Fabrication Techniques on Marginal and Internal Fit of Interim Fixed Dental Prothesis. Future Dental Journal. 2023; 9(1):65-72. doi: https://doi.org/10.54623/fdj.90111.
DOI
https://doi.org/10.54623/fdj.90111