Journal of Engineering Research
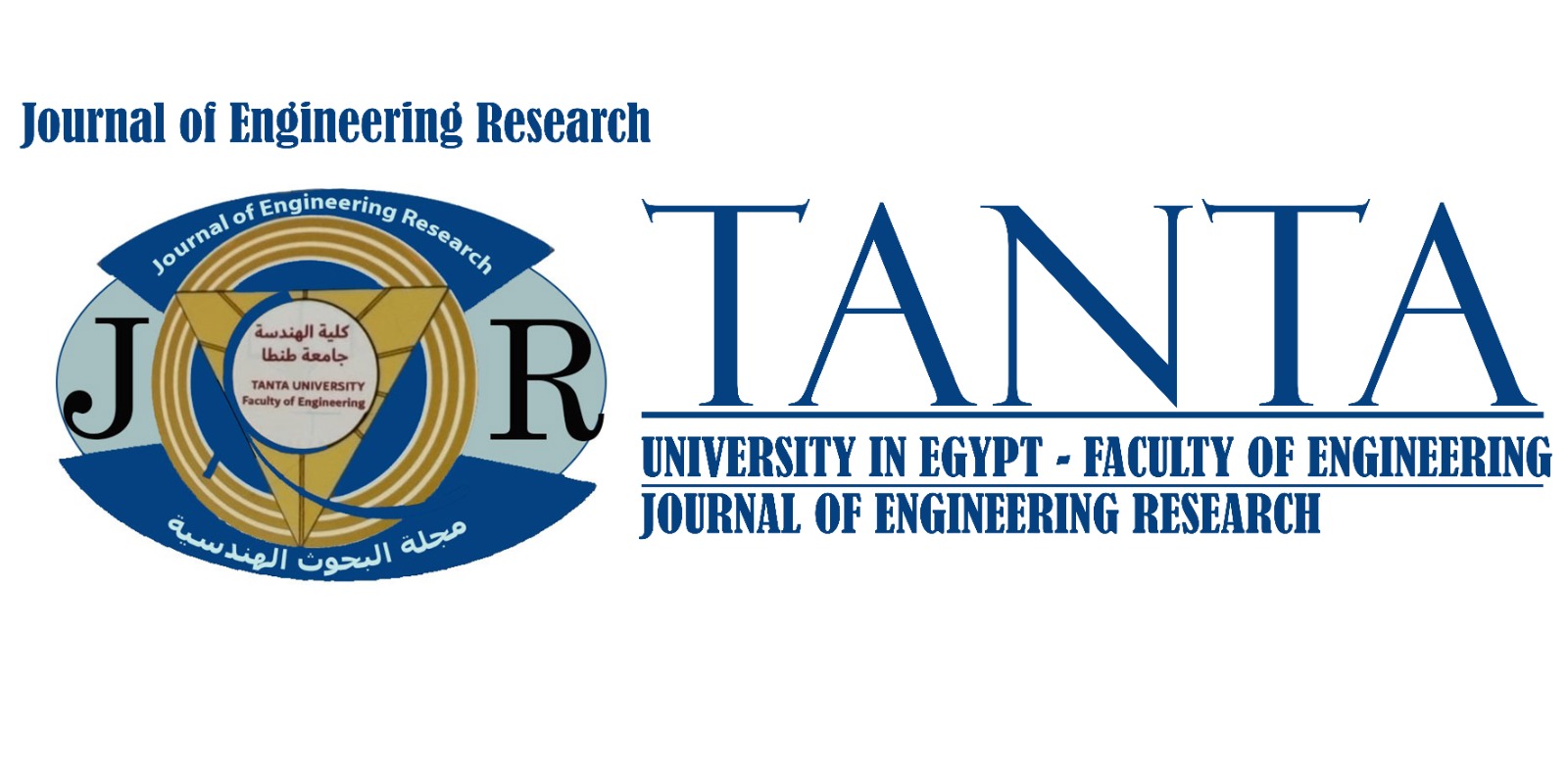
Abstract
The aim of this work is to study the effect of heating the FSW tool by means of an induction heating on joint strength during joining of polycarbonate (PC) sheets. This material was selected due to its transparency as well as its good photoelastic properties. Therefore, the defects can be easily detected and the residual stresses can be revealed under a polarized optical microscope. Four levels of suggested welding parameters (pin temperature, rotational speed and welding speed) were investigated. Both the mechanical properties and the defect formation were studied in order to achieve a better welding joint. The investigation of samples macrostructure showed that several defects such as islands of melted and non-melted material, discontinuous bonding line, macro-cracks, tunnels, flash formation, surface grooves, voids and root defects were formed as a response to the different interactions between the welding parameters. These defects can be minimized when the welding process is performed at a rotational speed of 1800 rpm, welding speed of 30 mm/min and tool temperature of 50 ◦C. In this situation, the joint efficiency of the welded joint reached 92.2% relative to the base material flexural strength.
Recommended Citation
Abdelmohsen Omer, Mohamed
(2022)
"Friction Stir Welding of Polycarbonate Butt-Joint: Defects and Remedies,"
Journal of Engineering Research: Vol. 6:
Iss.
2, Article 9.
Available at:
https://digitalcommons.aaru.edu.jo/erjeng/vol6/iss2/9