Journal of Engineering Research
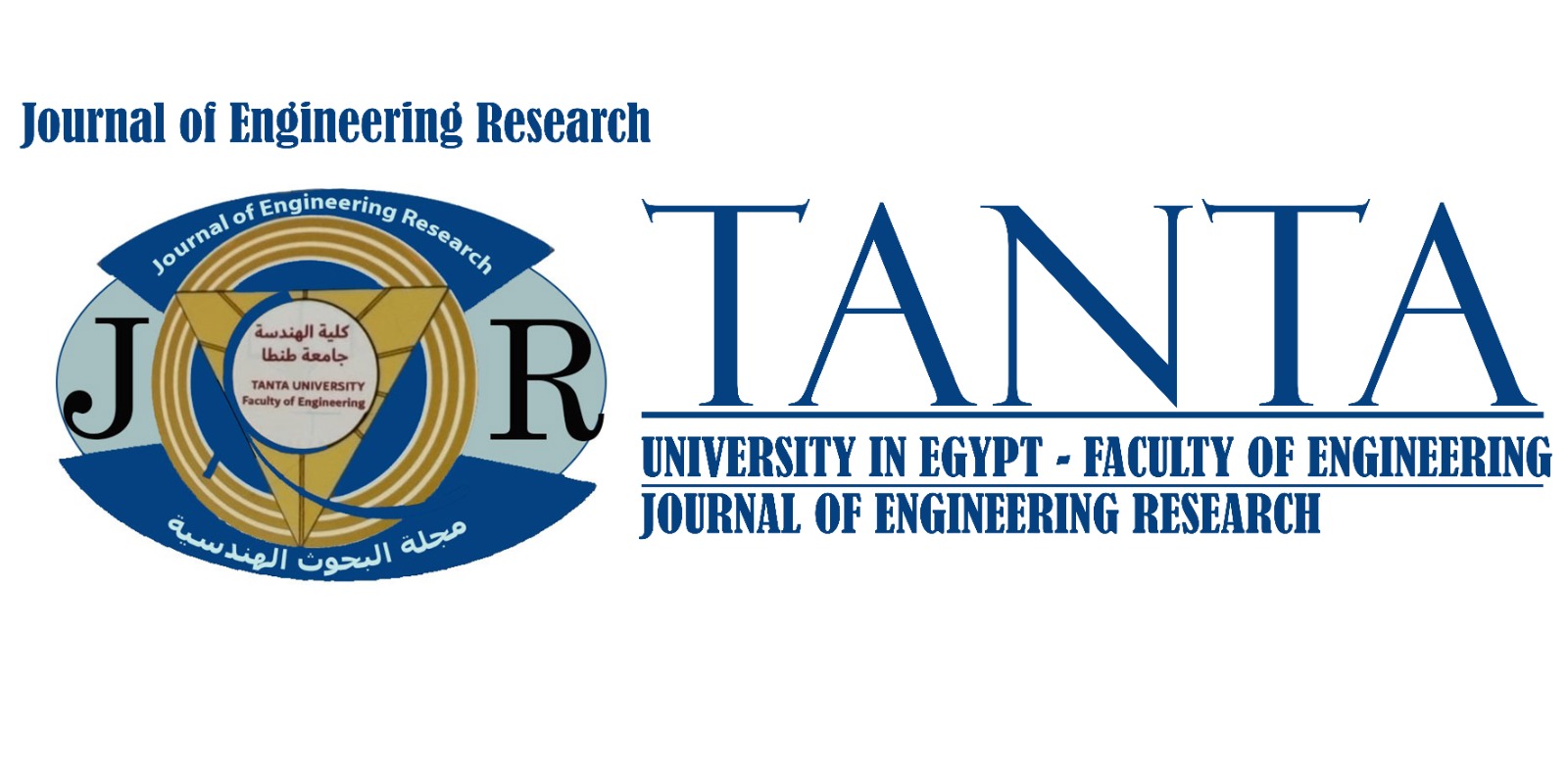
Abstract
A different models of Shell-and-tube heat exchangers were designed by Ansys geometry & Solidworks to evaluate the best model for heat transfer and to calculate the difference in heat transfer in each model by investigated with numerically modeling. Each model for heat exchanger has different assumptions for first model one tube & one pass with tube length 3 meter, was made with 2 different cases (each case have the same conditions such as same temperature, same velocity, changing the direction of the flow between parallel and counter flow). The flow and temperature fields inside the shell and tubes are resolved using a Ansys CFD 17.2. A set of CFD simulations is performed for a single shell and tube bundle and is compared with the experimental results. the Realizable K-ε model is known for predicting the flow separation better than Standard K-ε. The temperature of each model is examined in detail. Each design was studied separately on the basis of the findings, the designs need modifications to improve heat transfer. The main goal of designing these models is to obtain highest performance for shell and tube heat exchanger with given conditions. These studies were carried out to find the most suitable conditions of operation in shell and tube heat exchanger so that in the future it can improve the performance of heat exchanger in industries through applying these conditions.
Recommended Citation
Abdelhamid, Heba
(2022)
"CFD Comparative study of Design and Performance of shell-and-tube Heat Exchangers with different configurations,"
Journal of Engineering Research: Vol. 6:
Iss.
3, Article 33.
Available at:
https://digitalcommons.aaru.edu.jo/erjeng/vol6/iss3/33