International Design Journal
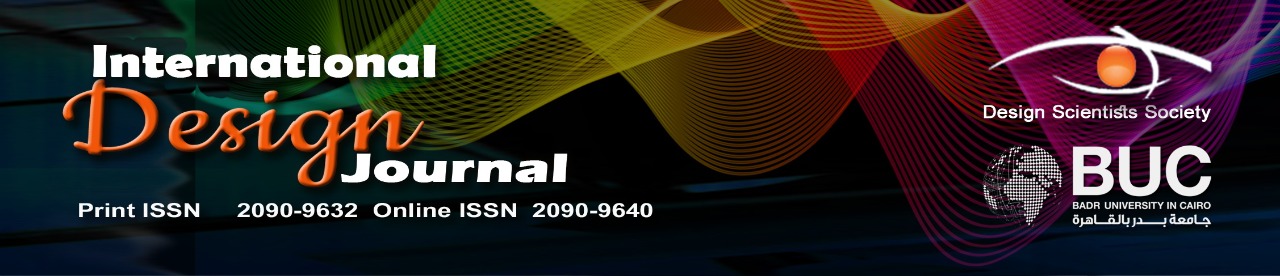
Abstract
The surface of the metal product is the first attraction factor for the user, as it is the first thing that he sees and interacts with it by his senses, which means that increasing the quality of the surface increases the competitiveness of the product in the local and international markets, and working on the quality of the surface of the metal product requires the designer to identify the quality standards of the surface of the metal product. It can be achieved by improving the shape and performance elements of the surface of the metal product. Finishing the surface of a metal product is one of the most difficult processes for manufacturing the product because of the skill and accuracyit requires, so the designer must study it and its developments to be able to determine the finishing processes appropriate to the nature of each product of the various metal products. In recent years, due to the properties it provides, it can improve the appearance and performance of the surface appearance of the metal product in addition to the possibility of developing it to obtain new properties such as self-cleaning . The surfaces of metal products traded between people are among the most vulnerable to damage due to the problems they face during use. Circulating these surfaces between users hundreds of times a day makes them vulnerable to corrosion by friction, and increases the accumulation of pollutants on surfaces and thus repeated cleaning operations, which also leads Corrosion, in addition to the presence of many metal products in a humid environment exposed to air, which also causes them to be exposed to corrosion quickly. Therefore, it has become imperative for the designer of metal products to search for modern and advanced covering methods to achieve the quality standards of the surface of the metal product and to acquire the new characteristics necessary to achieve this goal.. Research Queries: Do the physical evaporation deposition and electrophoretic deposition meet the surface quality standards of the metal product? Can physical evaporation deposition and electrophoretic deposition be used to give metal products the ability to clean? Objectives: The use of physical evaporation deposition and electrophoretic deposition processes to give the surfaces of metal products the Self-cleaning ability.Comparison between physical evaporation deposition and electrophoretic deposition processes. Research Importance: The importance of the research lies in the attempt to take advantage of the processes physical evaporation deposition (PVD) and electrophoretic deposition (EPD) to achieve the surface quality standards of metal products by providing them with the ability to self-cleaning, which increases the competitiveness of the metal product in the local and international markets. Research Methodology: Descriptive analytical method and Experimental method . Results: The surface quality of the metal product is governed by specific standards that must be observed. The physical evaporation deposition technique has the ability to produce a wide variety of colors but the resulting damaged products are difficult to recycle. Deposition by electrophoretic is characterized by its ability to paint complex geometric shapes, but it is difficult to use in achieving color plurality on a single surface. Titanium dioxide nanoparticles have a self-cleaning property. EPD deposition processes can be employed to obtain self-cleaning layers by treating only matte surfaces. The nanostructured titanium dioxide film is self-cleaning and is suitable for treating the surface appearance of matte and shiny metal products. The PVD operation system is a complex system that requires high skills and precision, while the EPD operation system is simple. EPD deposition uses environmentally friendly organic materials while PVD deposition negatively affects the environment. The use of nano titanium dioxide in surface treatment of metal products reduces the accumulation of pollutants on the surfaces. Nanostructured films can be obtained by using one of the PVD processes, which is the sputtering process
Recommended Citation
Ahmed, Mohamed Shohdy; Sabry;, Ahmed Mohamed; Mamoun, Mamoun ; Abdel Hameed; and Abdel Rahman, amal Abdel Razek
(2021)
"Employing the physical evaporation deposition (PVD) and electrophoretic deposition (EPD) processes in enhancing the durability and sturdiness of product surfaces.,"
International Design Journal: Vol. 11:
Iss.
3, Article 37.
Available at:
https://digitalcommons.aaru.edu.jo/faa-design/vol11/iss3/37